This article is a joint reflection by Loïc Petit, Enterprise Mobility Client Director, and Sam Waes, Business & Innovation Consultant, at Orange Business.
What is Industry 5.0?
The world is changing.
While industrial companies are currently looking to process improvements based on data-driven insights drawn from asset and equipment monitoring, the next wave of transformation places more priority on what employees need. Industry 5.0 recognizes the value of human workers and the need to transition business models towards a sustainable, human-centric, resilient society.
The European Commission argues, "To remain the engine of prosperity, industry must lead the digital and green transitions. Industry 5.0 provides a vison of industry that aims beyond efficiency and productivity as the sole goals and reinforces the role and the contribution of industry to society."
Historically, industrial revolutions focus on improving processes, with less attention paid to the humans who must work with new technologies. Industry 4.0 initially focused on automation at the expense of human workers, but business leaders now see automation without the human touch as an error. Elon Musk famously embraced automation at his Telsa factories but now says "humans are underrated."
Sam Waes, Senior Business & Innovation Consultant, Orange Business
That means bringing together sometimes incompatible solutions from a multitude of devices, contracts, services and service providers within an integrated platform to enable process and workflow automation in support of your workforce. Resolving this complexity typically requires Multisourcing Services Integration, which we specialize in. To achieve this, we leverage our knowledge as an operator and our understanding of business and tech to help consolidate all these different elements. This removes complexity and enables IT to support and augment business practice.
Digital everything, digital everyone
With every business now a digital business, workers across your organization are connected. The connected deskless experience extends to all categories of work, from management to frontline delivery and manufacturing employees. Such digitization of business processes can, for example, automate basic CRM tasks, enabling employees to focus on delivering high-quality customer contact rather than time-wasting repetition. Car manufacturer Volvo has equipped mechanics with Apple Watches and iPhones to improve productivity and answer customer questions.
But technology is a tool, and emerging industry wisdom says it is best applied with a human touch. Humans are good at handling multiple concurrent tasks, at reasoning, empathy and predicting events. Connected machines can augment these skills, adding pattern recognition, automating repetitive and dangerous tasks, and otherwise enabling humans to achieve more.
Industry 5.0 is all about digital processes that support humans, which means these must meet humans where they are. Every company is different, which means there is no unified deployment model. The devices used are perhaps as variable as the scenarios they face. Wearable, handheld, rugged portable devices and even the humble barcode reader are all in use, supplementing notebook and desktop computers. Each of these endpoints has purpose, gathers data, and can also pose security and integration challenges.
Of course, in addition to managing these devices, Orange also provides network support to connect mobile computers in use by frontline staff across numerous industries: manufacturing, warehousing, logistics, healthcare, customer service, construction and more.
What about the employee experience?
Critically, these solutions require employee engagement. Digital Employee Experience Management (DEM) is critical to this. Connected or non-connected, chosen by an employee or company-mandated, you can't imagine that simply equipping employees with technology will be enough for them to engage successfully. Companies hoping to achieve positive ROI must consider the problem – and the most important first step when attempting to augment human workforces with technology is to find out what your workers need. Deeply consider what the technology is meant to achieve and work with staff to develop digital experiences that meet those business goals in ways that do not create additional friction.
An employee experience is as important as the customer experience because improving it helps achieve better outcomes. And one guaranteed way to join the 85% of digital transformation projects that fail is to create solutions employees won't, or can't, use.
"When employees generate their own ideas about where digitization might support the business, respondents are 1.4 times more likely to report success," McKinsey & Co report.
The Orange approach was to engage directly with employees using various touchpoints to identify technology solutions to business challenges that had relevance to staff. This enabled us to support 90,000 of our own remote employees during the pandemic. This service integration approach also helps us support our clients, including large global enterprises with tens of thousands of employees.
Assessing DEM requires context and sentiment data. According to Gartner, "Despite significant digital workplace investments, most IT leaders are unable to measure digital employee experience." At best, delivering good employee experiences may become a "strategic differentiator that can reduce overhead and improve experience." In our own experience, these projects should begin with your front-line employees. An LNS Research report describes the mission as being one in which enterprises must seek to "…digitally integrate frontline workers into the overall operational management system."
Managing complex deployment scenarios
The scale of some of these deployments is vast. The largest corporations equip tens of thousands of employees with a range of different connected devices, but each deployment brings its own administrative challenge. Different device models, warranties and associated contracts all require management and inefficiencies can emerge as complexity grows. Security a major consideration, each device is an endpoint, and needs protecting.
But device management in an increasingly connected mobile enterprise isn't just a problem of device management, it is also an opportunity. While we know these solutions can augment human capability, the data they gather can expose fresh business opportunities and help realize CSR targets. Properly managed devices last longer, reduce IT-upgrade and support costs and help achieve environmental targets. Businesses need devices that last longer, use less energy, and deliver on environmental commitments in the current environment. They also need device management systems to identify business-critical problems before they impact your enterprise.
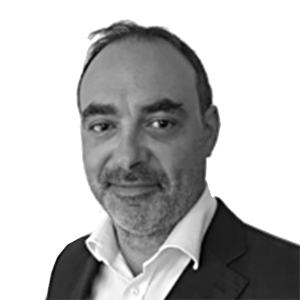
En tant que directeur clientèle au sein de la division Services de mobilité internationale, j’aide les entreprises clientes à identifier les solutions pour leur environnement de travail mobile, et à relever les défis liés à la gestion des terminaux devenus critiques pour leur activité.