Gartner defines a digital twin as “a software design pattern that represents a physical object with the objective of understanding the asset’s state, responding to changes, improving business operations and adding value.”
The concept of digital twins has been around for a long time. NASA used a digital twin to simulate the on-board environment on Apollo 13 back in the 1970s. The arrival of the Internet of Things (IoT), however, has now made digital twins a cost-effective model for business. According to Gartner, 13% of organizations using IoT are already using digital twins, while 62% are either in the process of establishing digital twins or plan to do so.
Application and business intelligence experts can use digital twins to decrease complexity in their IoT ecosystems, for example. The twin can continuously collect data from sensors, updating itself to mirror the physical thing. A digital twin can help engineers identify problems on a manufacturing production line and even help to mitigate the problem going forward. Utility companies can run a digital representation of a power grid to improve efficiency. Digital twins can also save on design and testing costs and so forth. Digital twins are invaluable at helping humans make decisions, or they can be automated to make decisions themselves.
Gartner forecasts that in 2022, over 75% of companies implementing IoT will have at least one digital twin in production. This rapid growth in the technology is down to awareness campaigns by technology vendors, but also because digital twins are offering up business value, which is making them central to enterprise IoT and digital strategies, according to Benoit Lleureux, Research Vice President at Gartner.
“We see digital twin adoption in all kinds of organizations. However, manufacturers of IoT-connected products are the most progressive as the opportunity to differentiate their product and establish new service and revenue streams is a clear business driver,” explains Lleureux.
The rise of the digital twin
The starting point for using digital twins differs according to enterprise size, industry and requirements, but the benefits are similar, according to Jeff Hojlo, Program Director, Product Innovation Strategies at IDC. These include clear communication, rapid collaboration, holistic visibility, efficient response to demand, closer collaboration with customers and monetization of IoT data in terms of predictive and proactive services.
Digital twinning is driving Industry 4.0, reducing time to market for new products, for example. In the product development cycle, manufacturers can use digital twins to develop and test products without the high costs of creating physical prototypes. At the same time, engineers can simulate and validate mechanisms, such as the brakes on a vehicle. Maserati created a digital twin of the Ghibli car using the Siemens PLM software platform. The digital twin played a central role in the development of the car, cutting both development time and costs. Finnish company Konecranes, specializing in the manufacture and service of cranes and lifting equipment, is using the same platform alongside Siemens’ Mindsphere open, cloud-based IoT operating system to build digital twins and reduce the number of physical prototypes, cut back on development costs and accelerate time to market.
Digital twins – reaching business goals faster
A smart connected product with a digital representation can be a real boon for business. It can increase an enterprise’s ability to make smart data-driven decisions, increase efficiency and avoid potential issues, such as assembly line downtime or problems with a car’s electronics when it reaches the future production stage. It also enables enterprises to experiment and innovate without adopting a costly fail-fast approach with physical prototypes.
As technologies that enable digital twins become more cost effective, enterprises across industries are finding ways to benefit from connecting the physical with the virtual through simple design and testing and what-if scenarios, for example. Take French supermarket chain Intermarché, which is connecting shelf store data to digital twins of the stores. The concept provides real-time indicators of stores’ performance and tests the efficiency of store layouts and product placements. Store layouts can be altered accordingly to improve product location and sales.
The development of digital twins
The popularity of digital twins will grow, forecasts Gartner, as they possess unique capabilities that can dramatically decrease the complexity of IoT ecosystems while significantly increasing efficiency. Their economic value, however, will fluctuate widely depending on the business case. Digital twins have the potential to cut development costs, speed time to market and assist in long-term asset management, but it is important to understand that they need a continuous diet of data to produce desired results.
Discover the technologies that are shaping the factory of the future, and read this exclusive Industry 4.0 whitepaper from Roland Berger containing interviews with manufacturers at the cutting edge.
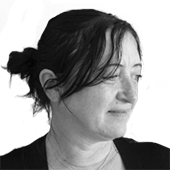
Jan has been writing about technology for over 22 years for magazines and web sites, including ComputerActive, IQ magazine and Signum. She has been a business correspondent on ComputerWorld in Sydney and covered the channel for Ziff-Davis in New York.