The answer to the first must be “yes.” Effective deployment of data-driven solutions has already enabled cost reductions in terms of machine uptime, effectiveness and use of consumables. Double-digit savings have been demonstrated in individual applications and in factory-wide systems wherever they have been applied, whether in Europe, the Americas or increasingly, China.
Internet of growing things
According to Accenture, the adoption of industrial digital technologies (IDTs) has the potential for a positive impact of £455 billion over 10 years1 to increase manufacturing growth by between 1.5 and 3 percent, to improve industrial productivity by 25 percent by 2025, to reduce carbon emissions by 4.5 percent and, far from costing jobs, to boost employment by 175,0002 – all these in the UK alone.
The smart factory will use artificial intelligence (AI) and other advanced technologies to improve productivity, profitability and quality and will be more agile than anything we have seen in large-scale manufacturing.
AI is going to increase, in extent and importance, but we will also see the growth of “cobotting” – intelligent machines and human beings working in an integrated way. A truly smart production process doesn’t simply use all the resources available, it optimizes their use.
Digital twins
Siemens is the Orange partner in developing industrial IoT solutions based on the MindSphere open IoT operating system. It defines a digital twin as a virtual representation of a physical product or process. This could be a jet engine or a factory line. They incorporate simulation, data analytics and machine learning capabilities to demonstrate the impact of design changes, usage scenarios, environmental conditions and other variables. They can help to reduce or even eliminate completely the need for physical prototypes. By collecting accurate data, the digital twin evolves and continuously updates to reflect any change to the physical counterpart. Lessons can be learned about real-world performance that can help to reduce development, enhance reliability and greatly improve the quality of products and processes.
The three types of digital twins identified by Siemens cover product production and performance. The design phase gathers physical elements and the physical bill of materials, along with virtual elements such as automobile software. It will effectively specify and determine engineering tooling.
The build phase helps to improve manufacturing, to tighten tolerances and boost the production cycle. Products in use experience different environments, different stresses and strains and their tolerances, fit and performance shift as a result. Sensors on products feed data to the digital twin, recording what is happening to them as they age.
Done correctly, digital twinning will influence the design, construction and operation of a device throughout a single life cycle. Informed service and support through the digital twin leads to fewer unscheduled downtime incidents and helps to improve performance in operation.
Digitization in action
Intelligent industrial communication networks provide for simple data exchanges within the different production modules and collect operational data on an ongoing basis.
The means and mechanics to collect data is widely available; sensors are almost at commodity-level prices. Software like Siemens’ Digital Enterprise Suite offers coordinated, integrated, automated and comprehensive solutions. The challenge is to use the data effectively: to sort the wheat from the chaff, in the first instance, and to act on it in the most timely manner possible. This is where the new and emerging technologies of Edge computing and 5G networks come in.
Edge computing
At first glance, edge computing reverses the trend toward the cloud – off-site servers, backups and data points. Edge is a “mesh network of micro data centers that process or store critical data locally and push all received data to a central data center or cloud storage repository, in a footprint of less than 100 square feet,” according to research firm IDC.
What is an “edge computer”? It’s not a new piece of hardware that is the next “must-have”; it’s a description of a connected item. Automobiles, airplanes and factory floor manufacturing machinery could all be considered as being “edge”; they are producing data for ongoing operation, on the one hand, and for analysis and improvement – through twinning, for example – on the other. Edge computing offers more effective management of enterprise data. It employs a “gateway” that effectively triages the information; it allows data from IoT devices to be analyzed “at the edge of the network” (hence the name) before being sent to the appropriate place – the data center or the cloud – or acted upon in the situation. Edge computing is about infrastructure that enables data to be processed as close to the source as possible. It facilitates faster processing and reduces latency.
5G
5G communications are integral to edge computing, effective digitization and the exploitation of the potential of IIoT and the Fourth Industrial Revolution. It is an essential part of the virtuous circle; its higher speeds, lower latency and greater capacity facilitate the IIoT, whose machines in turn are best placed to exploit and optimize the characteristics of 5G.
The bandwidth and higher speeds of 5G will enable smart factories to utilize robots more effectively and more responsively; the on-site, smaller and more dedicated data centers can make decisions more quickly, enabling fuller exploitation of AI. It also facilitates unmanned warehouse transportation to automate critical but time-consuming activities and processes.
5G can operate very effectively over short distances, making it ideal for operations to dedicated units, such as within factories. But it is also about delivering multiple network events over shared infrastructures through network slicing. Operators like Orange will be able to quickly generate and deploy customized “slices” of the network, tailored to customers’ individual needs – speed, latency, power output or whatever it is. 5G is set for a huge role in the near future of IIoT. That said, we will see a coexistence of 5G with complementing technologies. According to research by Ericsson and Arthur D. Little, 5G-enabled industry digitization revenues for ICT players will be $1.3 trillion in 2026, with the biggest potential manufacturing being accountable for about 20 percent of this.
Hurdles and obstructions
OEMs aren’t used to sharing their data, but in order to get the most out of interconnected factories, production processes and supply chains, it must be shared with collaborative partners and leveraged in real time.
The IIoT, powered by 5G, edge computing and digital twinning, provides the physical framework for 4IR. The opportunity is to connect everything in an effective way. Data is key; accessing it is the basic foundation, and analytics are essential to putting it to work, effectively and productively.
Find out how Orange can support your Industry 4.0 ambitions and read this Roland Berger Industrial IoT whitepaper.
1Accenture Report: 2017 Industrial Digitalisation Review Benefits Analysis
2MadeSmarter Review 2017 working group report on jobs and the economy (UK Government publications 2017)
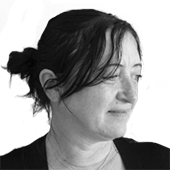
Jan has been writing about technology for over 22 years for magazines and web sites, including ComputerActive, IQ magazine and Signum. She has been a business correspondent on ComputerWorld in Sydney and covered the channel for Ziff-Davis in New York.