The manufacturing industry affects almost every part of our daily lives, from the shoes we put on our feet and the smartphones in our pockets to the cars we drive.
Manufacturers are continually looking at new ways to attract consumers, optimize processes, streamline supply chain and decrease costs. At the same time, like other industries, manufacturing is going through a huge transition driven by technology. To remain relevant in the digital economy, they must be more efficient and agile, while at the same time innovating and thinking smarter.
Gartner predicts that the global business intelligence and analytics market will hit $23 billion by the end of 2020. This is being accelerated by enterprises looking to use data generated by machines, sensors and people for real-time decision making. This includes smart manufacturing.
The untapped power of data
Due to increased, affordable computing power and advanced analytics, manufacturers can now exploit their treasure chest of data from multiple sources to enhance processes, increase supply chain efficiencies, reduce flaws and predict any areas that may affect production. Data analytics can improve product quality, for example. Huge savings can be made using predictive analytics in product testing. One product may require hundreds of quality tests. The number of tests can be reduced using pattern recognition and predictive analytics to determine the number of tests actually required, as opposed to blanket testing.
IDC forecasts that by 2020, 80 percent of manufacturers will extensively restructure, placing data at the center of their processes.
This wealth of data they have at their disposal, which many manufacturers still aren’t exploiting, can help them gain a real competitive edge, target new customers and make their entire operations more flexible and agile, from sourcing materials to the finished goods. This newfound awareness can also aid smart decision making and boost innovation. It can provide quick answers to previously complex questions, such as spotlighting unprofitable product lines quickly.
In order to optimize production quality and yields, for example, manufacturers require a continual data flow from production lines in real time to check for any inconsistencies and ensure all is running smoothly. This data coming from sensors on the production line can be linked with operational and financial data, providing smart information on any glitches and where production can be optimized and costs cut.
Big data analytics can enable manufacturers to quickly compare the production performance at different sites and pinpoint efficiencies. This data can also be used for growth strategies and the restructuring of production plants where it would be most beneficial.
To achieve this level of granularity, manufacturers need to know how to use their data wisely and analyze it to meet objectives. New analytics tools can’t deliver on their own. Manufacturers must also be prepared for a cultural shift, incorporating a change in people and processes to get maximum insight from their data. Employees, for example, need to know how to use data analytics tools to their true potential to establish them as a significant business enabler.
As McKinsey points out, introducing advanced analytics to manufacturing is a long-term commitment, not a one-off exercise. Analytics need to be repeatedly deployed to achieve valuable outcomes. This means rethinking business processes and integrating analysis tools into day-to-day operations, including curative and predictive maintenance.
The end-to-end data journey
From exploration to analysis, data runs through a complex journey. As a carrier-grade integrator, we understand how data needs to be orchestrated securely every step of the way to obtain maximum value and lay the foundations for Industry 4.0.
To help manufacturing companies be more data driven, we believe they need a robust strategic plan to follow six key steps: data collection; data transporting, storage and processing; analysis; sharing; disseminating; and finally, ensuring data is secure through the entire journey.
All of these contribute to the adoption of the factory of the future, which will have much more emphasis on collecting and producing data. Data intelligence harvested will influence everything from product innovation and design to production line sizes. Data can also be used to help carbon footprint by assessing power consumption and improving energy efficiency.
Manufacturers’ big data toolkit
Big data analysis is no longer a solution awaiting a tick on a wish list, it is now a critical part of any manufacturer’s toolkit. With the right solution, integration and management, manufacturers can finally leverage their vast amounts of big data to carve out a sustainable future that can help build a truly personal relationship with customers.
Find out more about our data intelligence solutions as well as solutions designed specifically for the manufacturing industry.
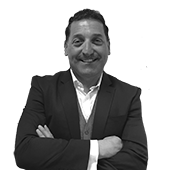
Lorenzo is the Managing Director for UK and Ireland, where he is responsible for the retention and growth of the UK business while ensuring Orange Business is recognized as the trusted digital transformation partner for all its clients. Prior to his Managing Director appointment, Lorenzo restructured the sales business to focus on driving new revenue growth across the strategic services portfolio. He also successfully evolved the new logo business, which has secured new prestigious customers, such as Google, BBC Worldwide and Jaguar Land Rover.