What is being done about it?
The International Council on Mining and Metals (ICMM), the representative body for the world’s mining companies, has committed to creating an international standard for tailings dams to be developed by an independent panel of experts. The standard sets out to review current global best practices in the mining industry and see where marked improvements can be made. Tom Butler, CEO of the ICMM, said, “ICMM CEOs have committed to creating a step change for the industry in the safety of tailings facilities by developing a recognized international standard for member companies.”
What else can mines do?
Digital technology can play a major role in improving tailings dam safety. The 4th Industrial Revolution (4IR) and Internet of Things (IoT) advancements have empowered industrial organizations, like mining companies, to gather data, analyze it, create insights and automate responses in entirely new ways – and particularly for tailings dam projects.
There is already existing instrumentation in place on tailings dams, but IIoT solutions mean mining companies can enhance that situation with automated data collection via arrays of IoT-connected sensors, enabling real-time data and the potential for intelligent insights.
The process for making tailings dams safer revolves around risk assessment, alerting, and response management: sensors and monitoring tools can be used to measure dam wall deformation, movement, and seismic and other vibrations. Pore pressure and water table levels can be measured using self-powered piezometers. Sensors can also measure dam and run-off water quality and concentration levels, while monitoring local environments can provide data on historical trends.
The best practice approach
In our experience and from a practical business governance perspective, securing tailings dams for the future can be best achieved using a set of best practices.
1. Organizational stewardship: put a clearly articulated strategy in place that sets out corporate governance for your facility, and then underpin it with training and competency-building programs for your employees. Having established this leadership, ensure it is maintained and practiced consistently.
2. Defined documentation and processes: establish clear processes for risk assessment, change management and any other procedures that are specific to your tailings dam, including things like general management of a tailings site, operations, maintenance and surveillance, and have an emergency response plan in place.
3. Best available technology (BAT): employ the philosophy of BAT to maximize your chances of avoiding tailings dam issues or potential incidents. BAT principles include eliminating surface water from impoundments, promoting unsaturated conditions in the tailings with drainage, and similar.
4. Defined roles and responsibilities: making sure job roles and duties relating to the tailings dam are clear and understood, again maximizing your chances of managing a tailings facility efficiently.
5. Review and assurance: carry out independent reviews, conducted by qualified and experienced third-party tailings professionals, to ensure you are doing all you can to minimize potential problems.
With the right partners
Not every mining company has the in-house capabilities to deliver on all the elements of a successful tailings dam management initiative. But working with the right partners can ensure that you do.
Operating a tailings dam successfully and safely means integrating strategic plans into existing instrumentation and systems while upgrading existing processes: this through the automated collection and aggregation of data and automated dissemination of real-time and historical insights, through multiple channels, be it to an operations center, a field engineer’s laptop or direct to the CEO’s smartphone. We believe our strategic Intelligent Insight Assets Alliance (IA)² with GHD Digital can help to deliver unprecedented value for clients assessing the end-to-end lifecycle of tailings dam management.
Why (IA)²?
The (IA)² partnership between Orange and GHD brings complementary capabilities that we believe will create new opportunities to meet the needs of our combined clients. GHD bring a business operations and industry subject matter expertise and track record that can help merge the IT/OT domains supported by Orange IoT solutions and experience managing the data journey to create a platform for Instant Intelligent Insights and real-time decision making. This value is demonstrable, measurable insights at speed that will help enterprises improve safety, be more efficient, decrease operational risk and create new revenues.
We can help achieve this using real-time visualizations and benchmark reports, driven by value-oriented business use cases: IoT solutions and connected sensors collect huge amounts of data from a tailings dam asset in real time and will continue to do so for the lifespan of the Tailings Storage Facility (TSF). Tailings dam operators who deploy automated collection and intelligent aggregation of data on sites give themselves a big differentiator. Tie that in to using centralized dashboards on site, structured workflows and alerting systems, all aligned to a business-defined Triggered Action Response Plan (TARP) framework, and the operation becomes still more efficient.
We believe in a principle of the right data, to the right person or people, at the right time and via the right channel. Conducting risk assessment and implementing a response management plan, with the right staff in place, can help mitigate the potential for failures in a tailings dam. Best practices ensure that you are always in a state of readiness to avoid those potential failures. And digital technology is the tool that will power it all now and in the future.
Thank you to all of the attendees at the Austmine 2019 event who came and met the combined GHD and Orange team at our booth. It was clear that the business impact and potential risk lens that needs to be applied to tailings dam failures has significant executive attention, and exploring ways to leverage IoT and deep mining industry expertise to solve these challenges is a priority for 2019.
Read more about how Orange can help you drive benefits from IoT and other digital solutions in the mining industry.
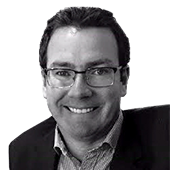