Smart manufacturing converges the physical and digital worlds. As part of this, simulation is providing engineers with the power to virtualize every phase of the product development cycle, speeding up design processes and making mass customization a reality.
To stay competitive in today’s digital markets, manufacturers need to reduce time to market and speed up new product development and production processes, while ensuring quality and efficiency. At the same time, they need to be flexible to customer demand.
Simulation is fast being adopted as a way of achieving these goals. It can be used for product design – to check whether there are any potentially costly faults with an initial prototype – as well as plant simulation so that production lines can be tested and optimized before they go live.
Take Nebia, a start-up that was looking to design a showerhead that would transform the user’s shower experience, while saving on both water and energy consumption. As most of the cost of a shower is in heating the water, the designers came up with the idea of atomizing the spray to increase the overall surface area the water covers by ten times, while reducing water consumption levels. Its engineers speeded up time to market using simulation tools, which allowed them to quickly test product variants.
Or consider sports apparel firms. They are looking to take 3D printing, which they have been using to prototype designs, mainstream to meet consumer demand for mass customization. Adidas, for example, is using 3D and 4D Carbon CLIP printing technology, which uses digital light synthesis to produce running shoes precisely engineered to an individual’s needs, drawing on data on their running style.
“For eons the manufacturing process has followed the same four steps that make up the product development cycle – design, prototype, tool, produce. Carbon has changed that: we’ve broken the cycle and are making it possible to go directly from design to production,” said Dr. Joseph DeSimone, Co-Founder and CEO of Carbon.
Playing factories
Many of us associate simulation with the world of gaming. IBM has managed to bridge the world of gaming and the smart factory via an interactive simulation game. It is designed to show how Watson, its artificial intelligence (AI) platform running on a supercomputer, can dramatically increase productivity. In the two-minute long “model factory” simulation, you take on the role of a shoe manufacturer and explore how production lines can use the Internet of things (IoT), analytics, machine learning and AI to double output, without doubling equipment and asset expenses.
The game opens with a request for an order: 2,000 blue and 3,000 tan shoe units. Everything in the smart factory is running smoothly until Watson’s weather alert suggests a blizzard is likely to disrupt the supply of tan materials. The player needs to decide how to get production back on track.
Next, a predictive maintenance alert highlights there is likely to be a system failure in the next 24 hours. Spoken feedback from the maintenance engineer is taken on board by Watson, which uses data analysis to find the root cause of the problem. Watson detects a failing part and asks the engineer to replace it. With no outages for the next 30 days, all orders are on time and budget.
It may not be as simple in real life, but the interactive game gives you an overview of how Industry 4.0, combined with intelligent sensors, analytics and AI, can optimize operations in real time.
Seeing double
Digital twins are becoming increasingly popular in the manufacturing space. They are basically digital representations of physical objects, operating virtually. They have enormous implications for both innovation as well as operational efficiency in smart factory environments.
Digital twins have the power to improve situational awareness and better respond to changing conditions, particularly when it comes to preventative maintenance and system optimization. According to analyst firm Gartner, they can also reduce operational and, in some cases, capital expenses by extending the life of an object, for example.
German manufacturer Siemens is using digital twins, simulation software and big data to advance manufacturing. It can simulate end-to-end production processes, analyze throughput and tweak machines where necessary. To increase quality control, it is able to use the digital twin to model changes on the fly before putting them into effect in the real world.
The way forward
Rising labor and system costs, alongside increasing customer demand, are putting more and more pressure on manufacturers. Simulation enables designers, engineers and executives to answer questions in a risk-free, inexpensive environment. For the smart factory owner, it really is a no-brainer.
Find out how you can increase speed and agility at every phase of the manufacturing cycle to achieve operational excellence and improve competitive advantage.
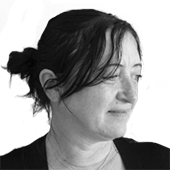
Jan has been writing about technology for over 22 years for magazines and web sites, including ComputerActive, IQ magazine and Signum. She has been a business correspondent on ComputerWorld in Sydney and covered the channel for Ziff-Davis in New York.