Edge computing is a technology deployment that puts applications and data as close as possible to the machines and users that need them. Many manufacturers we speak to opt for edge computing to process critical data on-premises, as the process is too lengthy to send to the cloud and avoids bottlenecks. Instead, less vital data is shipped to the cloud. For example, intelligent gateways at the edge enable data to be analyzed within the local facility, generating real-time intelligence for fast, smart decision-making. This data can also support predictive maintenance to address any issues before they happen, avoiding unplanned downtime.
Not only is processing data closer to where it is being utilized more efficient in terms of bandwidth, but it also reduces costs. The data should also be more secure, as it is being processed as near as possible to the point of creation.
IDC is predicting that by 2024, 70% of industrial organizations will run software-defined compute and network infrastructure for supporting information technology (IT), operational technology (OT) and communications technology (CT) functions at the operational edge.
Processing at the edge onsite, however, requires support. Retaining an in-house support team in all manufacturing plants is expensive. It is also difficult to source the skills locally. The answer is an integrated support model.
A single point of contact for support
An integrated support service provides a single point of contact and accountability for manufacturing plant managers, supplying expertise to help prevent issues from happening and deliver faster problem resolution.
The model provides local support for a manufacturing plant under one roof, lowering costs and complexity. Connectivity, security and data all sit under one umbrella. Plants don’t have to determine which vendor to go to if they have an issue.
When it comes to manufacturing infrastructure, any downtime is costly. Any disruption on a production line can result in significant loss for the business. At Orange Business, we can provide a one-stop shop for support in manufacturing plants, including governance and data at the edge. We are already in these factories, providing connectivity, for example, and we have partnerships with all the major vendors, including Microsoft for IoT Azure Edge and Dell Technologies Edge Computing.
One multinational customer came to us because they wanted an integrated support model for their factories to speed up their digital transformation. They did not want to spend time and money searching out individual support solutions for various software and hardware.
Shoring up security
Security has become a boardroom topic. Manufacturers don’t want to lose credibility by getting hacked, but they find it a real challenge to scale up. We have substantial expertise in this area through Orange Cyberdefense.
With our cybersecurity offering, for example, we can provide non-intrusive vulnerability monitoring that will at no point break the supply chain. We can separate IT and OT using specific firewalls to segregate connectivity and data flows.
Manufacturers are also having difficulties with governance. Some put OT into IT, so it comes under IT governance; others are unsure where to go. The truth is there is no one size fits all for OT/IT governance. The right governance model depends on how the organization and its culture are set up. Orange Business, as a carrier-grade service integrator, has experts in the field that can help with governance, management integration, reporting and measurement functions critical to the success of support delivery, for example.
We start with a consultative approach to understand the manufacturing plant’s security, connectivity, and where vulnerabilities are. We also look at your digital transformation maturity and what needs to be tweaked accordingly.
We can combine edge security and networking into virtual functions within a single support model. First, we monitor the OT/IT estate to see how big the risks are and then plan to mitigate the most significant risks; with legacy systems, we move services across to digital at a pace that suits the customer, in much the same way we did with telephony. An overall roadmap is created to support the move.
OT may already link to IT
In 2021, a plant operator in Florida had his system taken over by a malevolent actor looking to poison the city’s water supply. Access was gained via a remote desktop application to access the water facility’s central computer system. This highlights how IT and OT are already linked – and their interconnected relationship is growing.
SOAR (security, orchestration, automation and response) allows security teams to harvest data on information security events from multiple sources and analyze them, allowing for faster response and remediation. Coupled with contextual threat intelligence, which can accurately assist in evaluating threat levels and integrated with SCADA security solutions, industries can eliminate weak areas in the infrastructure, devices, configurations and traffic.
Of course, the arrival of 5G will not only supercharge OT/IT integration, eliminating the need for wired connectivity and creating greater flexibility. It will also bring with it security benefits in terms of "network slicing," which means it is easy to isolate parts of the network if there is an attack, for example. 5G private networks are also more secure by their very nature, making them appealing to industrial use cases.
The manufacturing industry is slowly realizing the value of 5G for automation, robotics and automated reality. By 2030, a recent survey maintains, manufacturing and industrial facilities will have 49 million 5G connections – but there is still a long way to go.
Simplifying vendor management
For the moment, manufacturers are increasingly moving workloads to the cloud and utilizing the edge to create new opportunities. But with new opportunities come new challenges. Managing support on-premises and in the cloud is complex. With multiple vendors, manufacturers can no longer turn to the simple "if it’s broken, fix it" model. They need a single-point-of-contact, flexible-support solution designed for their specific requirements.
We will see OT and IT consolidate within the next five years. But for the moment, support is an issue. Manufacturers need a trusted partner with a deep understanding of their industry, technology and business outcomes to provide enhanced support requirements that keep the production lines moving 24/7 and bolster the bottom line. Time, as they say in manufacturing, is money.
Find out how you can increase the agility and resilience of your industrial operations and learn more about security in manufacturing.
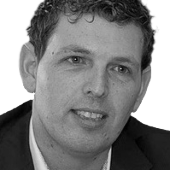
Dave van Meer is Head of Solutions at Orange Business in Netherlands. He brings 20 years of extensive leadership in the Consulting and Managed Services ICT industries. As in his career, he also values relationships in his private life and is people centric. He loves to spend time with his family and friends. His lifetime hobby and sport is volleyball, on the court and on the beach.