Smart city projects are booming throughout the Middle East and Africa (MEA) region. From Saudi Arabia’s $500 billion Neom smart city to Kuwait’s $4 billion ecofriendly Saad Al-Abdullah city, this part of the world is a hotbed of smart city ideas and initiatives. The smart cities boom has gone hand-in-hand with the rise of IoT. According to the GSMA, IoT revenues in MEA will reach $55 billion by 2025, while IoT will also grow MEA’s GDP by $18 billion by 2025.
Building smart cities requires a lot of valuable construction equipment. Most people would not necessarily associate IoT with diggers, earth movers, dump trucks and other heavy construction equipment typically found on construction sites. But for construction companies, IoT has become increasingly important in helping improve efficiency and reduce theft. In the U.S. alone, theft of construction equipment costs as much as $1 billion per year. IoT helps them manage these assets by tracking their location, performance and other operational metrics in real time.
How has it worked until now?
Asset management in construction companies has traditionally been a manual process. Inventories of site equipment would be maintained by hand on paper or in basic spreadsheets. Asset movement has also been traditionally hard to track, because assets tend to move around from site to site as needed. When a task is finished at one site, the machinery is moved to another site to perform a new task there. This meant that information on an asset’s location or condition could become quickly outdated before that information got back to the central office.
The net result of this was that tools and equipment regularly got lost or misplaced. Site managers would be unable to find vehicles when they needed them. Asset theft was commonplace. And not having access to timely, accurate data about the condition of assets meant inefficient use and consequently higher operating costs.
The benefits of real-time data in asset management
By equipping construction assets with IoT-connected sensors, companies are able to use digital asset tracking to monitor the location, movement and performance of their physical assets. Furthermore, by collecting data from these now-connected assets, companies can build a consolidated system for monitoring, tracking and analytics in asset management.
Operational efficiency is increased by being able to quickly pinpoint the location and nature of a fault in a connected system, for example. In addition, both efficiency and productivity are improved by being able to check inventory of devices without a human worker needing to manually monitor them on the construction site. Construction companies in the U.S. report spending 90 hours a month on asset searching, time that IoT asset tracking could help them put to better use.
And at the most fundamental level, construction companies working on smart city projects know that they are under huge pressure to avoid cost overruns and finish projects on time. Knowing the exact location of your whole asset inventory means you get to maximize equipment utilization by having the right equipment in the right place at the right time.
The predictive maintenance factor
In addition to tracking asset location, predictive maintenance is one of the key use cases for IoT-enabled asset management. According to a PWC report, predictive maintenance in construction companies could reduce costs by 12%, improve uptime by 9%, reduce safety, health, environment and quality risks by 14% and extend the lifetime of an asset by up to 20%. Historically, predictive maintenance has been impeded by poor asset location visibility and inefficient maintenance record keeping. IoT asset management, with its real-time equipment and vehicle tracking, overcomes that issue. If a construction company has assets deployed at multiple sites, it can instantly know the location of all assets, how they are being used and their maintenance status.
Properly maintained equipment keeps your teams in the field working more efficiently. It can also generate significant cost savings through reduced repair expenses and lowers the need for capital investment by extending the service life of vehicles and equipment.
Benefits extend to enterprises
It isn’t only industrial organizations that can benefit from asset management: enterprises in general can reap the rewards, too. All enterprises have assets that are of value to the business, and by having an asset management strategy, they can develop, operate, maintain, upgrade and dispose of assets cost effectively. Asset management can give a holistic view of an asset’s entire lifecycle, from procurement and implementation through to renewal and disposal. General benefits include a faster return on investment, the ability to measure improvements in operational efficiency, lower costs and better risk management: all of which are typically popular for enterprises.
A more organized, more efficient future
IoT asset tracking can help companies throughout MEA manage assets much more efficiently than they are doing currently. By having better visibility of asset location and condition, in real-time, companies can remove the time presently wasted searching for assets – be they tools, vehicles or equipment – from one place to another, and reduce equipment downtime through data and improved planning. You are then able to maximize employee and equipment efficiency and optimize any underutilized assets. And of course, it helps you track your assets and lessen the threat of theft of valuable equipment from sites.
Juniper research reports that global spending on asset tracking solutions will reach $33 billion in 2025, up from $10 billion in 2020. It is a technology that will grow and grow and continue to support IoT and smart city projects.
If you would like to talk about the topics covered in this blog or anything else to do with digital transformation in MEA, please contact me on: sahem.azzam@orange.com
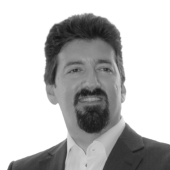
Sahem Azzam is Senior Vice President, Middle East, Africa and Turkey, leading the Orange Business team operating across the region comprising 60+ countries from the regional headquarters and Innovation Hub in Dubai, supported by offices in Egypt, Morocco, Nigeria, Saudi Arabia and the Arabian Gulf, South Africa and Turkey. He has a special interest and expertise in infrastructure services, IoT, Big Data, Smart Cities, Blockchain and IT service management.