The most recent report from the UN IPCC (United Nations Intergovernmental Panel on Climate Change) in early October emphasized that the need to switch away from fossil fuels is even more pressing than had previously been reported.
Experience tells us what the consequences of such a report will be: there will be new waves of stricter environmental legislation, with penalties for transgression and increased supply costs to encourage lower consumption. These will apply to all businesses, regardless of their opinion on man-made global warming.
Businesses that are going to survive and prosper don't need to be told to focus on making the best possible use of every unit of energy; they are already making it a priority. However, not every business knows how to squeeze every drop of value out of each kilowatt hour – and there is always room for improvement, even for those who think they are doing quite well.
Knowledge is power
In order to control how much is being used, we must know what is going on – and that requires data. The more we know, the better able we are to manage it.
We need to understand where we are wasting energy. The first places to look will be motors, followed by HVAC (heating, ventilation and air conditioning).
What we should seek is to run those systems to their maximum efficiency. In the case of motors, that is usually at about 75 percent of their capacity, depending on their function.
It is not unusual to find that motors are being run at 110 percent of their nominal power. So long as everything works, no one cares. The problems arise when something breaks down. Of course, oversized machines are much less likely to break down, but that doesn't mean they are efficient; they will still be consuming more power than needed. Whether the motors are running stamping machines, conveyor belts, compressors or anything else, get them monitored. Mount sensors and link them together in order to get the fullest, three-dimensional picture.
Similar principles apply to HVAC. As well as challenges with efficiency, spaces in buildings cool down, or they get too hot. Factories are big, open spaces. Does anyone have responsibility? Someone should – at board level.
There are plenty of passive measures that can be taken to improve basic building energy performance, and many businesses will probably have already installed most of them – insulation, pipe lagging, double glazing, automatic door closure, etc.
Get active
The real gains are to be made by applying Internet of Things (IoT) technology to measurement, monitoring and management. Businesses still must calculate the size of the building to be managed, their ceiling heights and so on in order to understand the challenge. But that process encourages critical analysis. Ceiling fanlights may be open – why? When? For how long? Would it be better to replace open windows with fans, either passive or powered?
Once the challenge is understood and the sensors and monitors have been fitted, you can get down to saving money. Schneider Electric has demonstrated massive savings in building energy performance with its EcoStruxure Building integrated strategy.
On the factory floor, sensors and monitors will identify where you are losing energy, in what form and why. Heat from a machine is the first indicator of waste. The optimal base heat emission should be established; machinery running hotter has got something wrong with it. This could be the wrong applications, too much demand or there could be a fault. Knowing there is an issue enables the problem to be remedied.
Once machinery has been audited, faults rectified and those past repair have been replaced, that heat which is still generated can be harvested for reuse elsewhere – in the HVAC system, for water heating or for pre-heating, for example.
If the machinery already has OEE sensors, the means of condition monitoring is already in place.
Change is going to come
Externally, management of supply – correlating demand and balancing generation and distribution – is very important, especially in the rural USA, where local, small energy companies distribute power to country areas.
Making the network smart enables more proactive and responsive switching of supply. I was involved with a start-up about nine years ago, which was established in order to put IP-enablement into power-consuming devices. The technology is already available.
Demand for electricity is high already and is going to get higher as coal and oil-fired generating stations are phased out, and vehicles move from internal combustion engine power to electricity and even higher demands on the grid. Workplace car parks will have more and more charging points; how will that demand be managed? How will unsustainable peaks be avoided?
New sources of power are not, so far, able to generate power as reliably and as powerfully as traditional fossil fueled power stations.
Smart grids
In order to make alternative power supplies reliable and sustainable, we have to move to what is being called the Smart Grid. Factories themselves will be expected to manage their power usage in a smart, proactive way; the Smart Grid will do the same thing but on a much larger scale.
A range of power sources will be required. Their management will have to be so responsive that artificial intelligence will do most of the heavy lifting, matching demand to supply in real time, moment by moment.
These grids are already starting to appear in parts of the UK, in other parts of Europe, in Australia and New Zealand, and in other parts of the world.
Orange works with customers in developing and managing a range of solutions that will enable today's power grids to become more responsive and tomorrow's to become genuinely intelligent.
These solutions are not optional; they are essential to a carbon-free economy. There are huge opportunities for producers of the infrastructure that will enable smart networks, such as Orange, but also for consumers, including businesses of all sizes.
Smart networks start with a single unit, whether it is a home, an office or a factory. Users can gain real benefits in costs, usability and efficiency by managing their power needs more efficiently. It would be commercially irresponsible to fail to do so.
Discover how Orange can help manufacturing companies with solutions for turning data into smart, actionable business information.
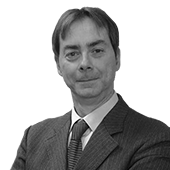
Before joining Orange Business, Pier Giuseppe Dal Farra served as Chief Operating Officer of ASTES4 SA, a Swiss-based tech company specializing in mechanical design and automation software. He was also cofounder of IPenable Inc., a company which pioneered the deployment of IoT in the Energy Vertical Sector. Today he is an IoT Industry Business Expert at Orange, focusing on all things IoT.