A host of companies around the globe have rapidly repurposed their production lines to meet shortages, from medical supplies to hygiene products. As well as bringing in valuable revenue in this fallow period, it has also flagged up their community-wide spirit in helping to combat coronavirus. Technology in manufacturing will benefit in the long term from such innovation and collaboration.
Drastic changes to product lines are not without challenges, from initial design through to production. Regulatory bodies need to be flexible where possible to support these manufacturers. The UK Government’s Medical and Healthcare Regulatory Agency (MHRA), for example, has published guidance on the “minimally acceptable” performance for ventilator designs.
Technologies such as advanced digital design and 3D printing have enabled companies to quickly start manufacturing visors for health professionals, for example. As manufacturers add “resilience” to their corporate objectives, technology will have an even greater role.
A more flexible manufacturing model
The pandemic has derailed production lines and supply chains. Social distancing and worker safety will add even more pressure on manufacturers as they ease back to work. Gartner believes that up to half of workers will be unable to do their jobs on site as a result. This will create a huge issue as most factories are not fully automated or designed to be operated remotely.
Manufacturers need to start acting now to quickly respond to new sources of supply and changing consumer behaviors, according to McKinsey. It sees digital capabilities as critical here, providing manufacturers with the “flexibility and resilience needed to mobilize in unfamiliar territory.”
Unlocking the value of Industry 4.0
Industry 4.0 will be pivotal to improving productivity, efficiency and agility – and ultimately the customer experience. Industry 4.0 and the Internet of Things (IoT) will increase automation, enhance communications and provide new levels of data analytics.
Smart, connected technologies that can enhance automation, machine-to-machine (M2M) communications, production-line monitoring, predictive maintenance and analytics for smart decision-making will be essential in providing the real-time intelligence manufacturers need for future resilience. Multiple sections of the production line can be enhanced to speed up production, switch product lines, improve quality control, create more personalized products and reduce downtime.
Industry 4.0 underpins resilience by providing real-time visibility into raw materials, workforce and products. Artificial intelligence (AI) and machine learning (ML) can be exploited to continually monitor and assess production plans. Augmented reality (AR) can speed up training for assembly tasks and assist with complex assembly and the maintenance of manufacturing equipment.
But Industry 4.0 is not a silver bullet. It comes with challenges for manufacturers. There are obvious security issues as more devices become connected. Protecting intellectual property and customer information is crucial. In addition, there is the big issue of IT and operational technology (OT) which have usually operated separately, in silos. With greater integration, both must collaborate to create a more secure environment.
“COVID-19 has altered our relationship with digital — where digitization was a “can” before the pandemic, it is now a “must.” Companies will need to accelerate their moves to automate processes from manufacturing to the back office,” explains Dr. Marek Rozkrut, EY EMEIA, Co-Chair Economists Unit.
Bring it back home
A desire to be more resilient and responsive has prompted manufacturers to reevaluate where their products are manufactured and by whom. COVID-19 has highlighted concerns about dependencies on manufacturing in other countries, especially when it comes to complex transportation logistics and supply chains. As a result, we will see the re-establishment of domestic manufacturing in some sectors.
Governments will inevitably see this as a route to greater sustainability for critical supplies and hitting environmental targets. In a recent EY survey, 57% of enterprises said they would increase “focus on sustainability and climate change.” As a result, 83% said they expect a move to nearshoring, and 56% said they expect a “reversal in globalization” through major supply chain restructuring for greater agility.
For manufacturers in high-cost countries, such as Western Europe, to consider nearshoring, they will need to bring down the cost of production with increased automation. “Robotics will help optimize operations, reduce cost and increase speed. Increasing resilience may require restructuring and diversification of some supply chains. All of these will require structural change and investment, but technology investment, in particular, should accelerate,” says Rozkrut.
Designing resilient supply chains
One big lesson we have learned from COVID-19 is that resilient supply chains are crucial. To establish them, manufacturers will need to implement and regularly update robust risk management and business continuity strategies focused on risk assessment and remediation.
“Processes and tools created during the crisis management period should be codified into formal documentation, and the nerve center should be a permanent fixture to monitor supply chain vulnerabilities continuously and reliably,” says McKinsey.
McKinsey believes that over time, stronger supplier collaboration can also help to reinforce the whole supply chain ecosystem for greater resilience.
In this quest for supply chain resilience, EY noted that 80% of executives plan to transition to lean or additive manufacturing such as using 3D printing to gain advantages in “speed, cost, precision and materials.” Technology will also contribute to keeping operations and supply chains open by improving health and safety and reducing human-to-human interactions.
A smart future
In this emerging low-touch economy, manufacturers will need to build themselves digital-first operations. They will need clear visibility of their operations, order status, inventory and supply chains, which can be swiftly changed to deal with any disruption in the future. This will require a major re-think of the manufacturing process, technological innovation and stronger collaboration across the supply chain.
Industry 4.0 depends on a degree of IT-OT convergence, and that can throw up new security risks. Read this exclusive IDC research note: The Road to Digital Transformation: Enabling OT-IT Convergence, which looks at the positive steps that you can put in place in order to make security a cornerstone rather than a stumbling block.
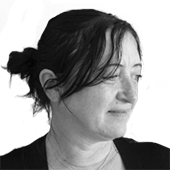
Jan has been writing about technology for over 22 years for magazines and web sites, including ComputerActive, IQ magazine and Signum. She has been a business correspondent on ComputerWorld in Sydney and covered the channel for Ziff-Davis in New York.