Talk to anyone who coaches children to play soccer, and you’ll no doubt hear them complain that many of their players want to try the tricks and skills they see their idols performing in the Premier League or World Cup. The basic skills aren’t appealing.
Yet it is only by mastering these fundamentals that star players can pull off the seemingly impossible. Only as the children grow up and their knowledge of the sport matures can they begin to understand the importance of having a solid foundation and why the best players are those that can do simple tasks well.
Going back to basics in the digitalization of manufacturing
We see a similar thing in manufacturing. Businesses know they need to transform digitally. They want to reap the benefits of Industry 4.0 by being more agile and responsive, predicting what will happen and acting to seize opportunities and avoid problems before they occur. It’s not hard to see why: McKinsey estimates that successfully implemented digital solutions can deliver 30-50% reductions in machine downtime, 10-30% increases in throughput, 15-30% improvements in labor productivity, and 85% more accurate forecasting.
But for many, that’s the equivalent of successfully scoring a goal with a bicycle kick from the halfway line. Manufacturers that reach that point are operating in what’s known as the data age, the third stage of the journey they undertake to make the move from Industry 3.0 to 4.0.
Before that is optimization: being able to calibrate machinery, predict failures and perform maintenance when it is needed, not when it is scheduled. And before that stage comes, stabilization or getting the basics in place. It’s a lot of work, but it is a critical element of a successful digital transformation.
The good news is that most will see value just from building those foundations. How? By focusing on overall equipment effectiveness (OEE).
Improving effectiveness before digitalization
OEE is not a new concept. It’s been used to measure manufacturing effectiveness for some time. It is calculated by multiplying machine availability, production performance and output quality to create an OEE score or percentage. The closer to 100%, the more effective the overall manufacturing process.
But despite not being new, OEE is still theoretical for many organizations. They may well be aware of it, but they have yet to implement it fully. We find that those who have yet to start tracking OEE generally score in the 30-40% range.
World-class manufacturers typically score above 90%, which means those businesses just starting out have an opportunity to double their capacity for effectiveness. So, even before they begin their wholesale digital transformation, they will have significantly increased their availability, performance and quality.
And they will have done it in a way that is producing volumes of standardized data – exactly the fuel needed to power the next stage of their journey or the optimization of their assets.
From stabilization to optimization
It is here that manufacturers go from having a high OEE in optimum conditions to proactively tackling problems before they occur. A manufacturer might have an OEE of more than 90%, except when it is time to maintain the machinery. Because they operate on scheduled maintenance, they must stop various processes, necessarily affecting output. However, by using the data they’re now generating, the manufacturers can start to predict when maintenance might be required and plan any interruptions to coincide with when demand is expected to be lower.
This is only possible if all the services and applications a manufacturer uses – from customer relationship management (CRM) to enterprise resource planning (ERP) and manufacturing execution systems (MES) – talk to each other.
To a degree, this already happens – most manufacturers have various systems at different stages of digitalization, with some automation. So, CRM may talk to ERP, which may in turn, talk to MES. But the data shared may come in different formats, and time is lost as data is reformatted to meet the requirements of the next system. That’s before we consider there may be integration issues that make the flow of data between systems inconsistent.
So, to get to that point of quick decision-making, of proactivity and identifying issues before they occur, manufacturers need to find a way of getting systems to talk to each other. This is where Unified Name Space (UNS) comes in. A messaging system that connects production equipment, applications and information. Rather than trying to connect systems to each other, each asset or application talks to the UNS, which in turn sends back relevant information.
For example, CRM data feeds into the UNS, and then whatever’s relevant to other applications is shared with them, rather than going through an ERP. So, a major order could come in, requiring three machines to work at full capacity for a week. In the past, this would have been fed into the ERP, production would have been planned, and there might have been a clash with scheduled maintenance on one of the machines. This could have delayed the order, but due to the drawn-out way in which data was shared, the customer might not have been notified of the hold-up.
The third stage of digital manufacturing
Now, however, that order information is being assessed alongside machine capacity, plans for maintenance and other inputs, and a production schedule developed and deployed and is constantly adjusted as it interprets the data. If that means it might take longer to deliver the order due to capacity constraints, that information will be fed back to the CRM, with the ability to update the customer rapidly.
This is the beginning of that third stage, the manufacturing digitalization equivalent to the bicycle kick: the data age. At this point, they will start to see the accelerated benefits McKinsey highlighted. But it is only possible if businesses get the basics in place first.
From assessing digital transformation maturity levels to helping implement UNS, Orange Business has the skills and expertise to support manufacturers, no matter what stage of the digitalization journey they have reached. To find out more, please contact us to discuss further.
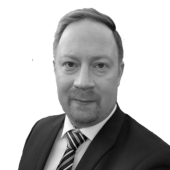
Johan, IIoT & Industry 4.0 Solutions Architect at Orange Business, architects digital solutions for industry, working with manufacturers to do more with less and always investing in creating value as the means of explaining why architecture is important. Outside of work, he enjoys spending time with family, eBiking, skiing, ice skating and learning to play golf.