Why does this happen?
There are many reasons, but it could well be that there is too much focus on technology. This might seem counterintuitive for projects based on increasing the use of technology within an organization. Yet our experience at Orange Business suggests that four out of five transformations that impact users fail when the primary focus is technology.
The people factors delivering transformation success
It could be argued that technology should be the third priority in a digital transformation, behind process and people. When McKinsey analyzed the critical factors in successful projects, many were people focused. Each factor could be placed into one of five categories: having digital-savvy leaders; workforces with the right capabilities; empowering people to work in new ways; frequent communication across a range of channels; and upgrading day-to-day tools. Of those, only the last could be considered primarily technology focused.
What does this mean for manufacturing, an industry in the grip of both intended and unforeseen change?
With the focus on sustainability, skills shortages, supply-chain shortages and unpredictable consumer demand, it is unsurprising that many manufacturers are investing in transformation. They are looking to improve production, streamline distribution, cut waste and emissions and, ultimately, supercharge growth. A Gartner survey of manufacturing leaders identified digitalization as the joint top issue CEOs were pushing their teams to focus on.
But while many are heavily invested in different transformation projects, they are not immune to the issues affecting other sectors’ digitalization efforts. In other words, they are just as susceptible to failure if they have not focused on encouraging employees to actively engage in driving change.
Overcoming a preference for the status quo
Few people are comfortable with change. The uncertainty that it brings worries some people, whether it is about losing employment, frustration that tasks are disrupted, or time and resources are not available.
These elements can all contribute to anxiety in the workforce. This increases the risk of employees not committing to the change themselves (thereby threatening the success of the transformation), or even exiting the organization. Digital transformation must rank as one of the most significant changes an organization can undertake. It challenges familiar tools and processes, replacing them with new ways of working. Unsurprisingly, people are often resistant to the change it demands.
Steps to engage workers
So, for manufacturers looking to successfully digitally transform, engaging the workforce should be at the top of their priority list.
First, whatever the change taking place, everyone affected needs to know how the transformation will add value to their daily jobs. Any project needs to answer the question of “what’s in it for me?” There is an opportunity here for manufacturers to ensure the project meets the needs of both business and workforce by involving employees at every stage of the project.
For instance, one manufacturer deployed trainees as “digi-scouts” on a project to improve how information can be provided to employees using augmented reality glasses, tablets and smartphones. The digi-scouts experimented with tools they were familiar with to create the content while working alongside other employees to gather detailed knowledge on existing processes and systems.
The result was that trainees felt like they had a real impact on the business, the manufacturer was able to deploy new technology to improve workforce efficiency, and users were confident that the tools and content would improve their ability to do their jobs. Furthermore, these trainees helped older employees to onboard this smart-factory project in a reverse mentoring process, establishing a “Smart Factory is 70% mindset,” explained Ingo Hild, Plant and Operations Manager at OSRAM, who was driving this project in his factory.
Second, understand where true leadership lies and get it onside. Buy-in from the C-suite and other decision makers is key, but every organization has unofficial leaders and influencers. They might not hold a senior job title, but winning these people over and getting them involved in the transformation can make selling it to the wider workforce much easier.
Building resilience and attracting and retaining talent
Of course, following this process for every transformation can be time consuming. More efficient would be to devise a way of changing the organizational culture permanently to one that can easily assimilate future changes without significant disruption.
What’s needed is to build up an organization’s emotional resilience – the ability of its workforce to easily adapt to difficulties and perform well in various situations. It is based on high levels of emotional intelligence: that ability to understand and manage your own emotions and those of the people around you.
If employees become more emotionally aware, they can recognize what they are feeling, why they are feeling it, how it might affect others, and how they might feel. This, in turn, helps them express themselves better—and employees who are comfortable expressing their feelings can release a lot of tension and avoid a fight-or-flight state, which blocks learning and creativity. In a safe environment, they will feel empowered to experiment and trial new approaches, leading to innovation or uncovering better ways of working.
Instilling emotional resilience in a multinational manufacturer
It was precisely this need for emotional resilience that led Airbus to implement its + Emotional energy@work initiative. Launched in 2015, the program is designed to boost emotional intelligence and organizational resilience through a series of talks, events, conferences and workshops for employees, underpinned by a dedicated intranet system.
A good example of how + Emotional energy@work has helped develop emotional resilience comes from returning to work after the pandemic. With some employees expressing safety concerns, Airbus could use the initiative to gather their thoughts and communicate how it implemented measures to address issues. Employees felt listened to, and engagement levels remained high when other employers struggled with the challenge of returning to the workplace.
Driving cultural transformation
The challenges manufacturers face demand digital organizations that can adapt to significant, continuous disruption. This requires both technical and cultural transformations. Without getting employees onside, manufacturers will struggle to drive user adoption of the new measures or hold on to the staff they need to achieve success.
Transforming the organization is imperative for manufacturers, but it can be daunting. Read how Orange Business has helped customers implement a human-inside approach to technology-driven change.
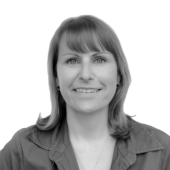
Carola brings 15+ years’ experience collaborating and leading intercultural and multilayered teams for ICT companies. She manages complex projects and diverse teams, empowering digital transformation / IIoT / Industry 4.0 initiatives to optimize operations, boost employee safety and ensure sustainable growth. In her leisure time, Carola volunteers for nonprofit organizations and enjoys traveling and meeting humans around the world.