Pour regarder cette vidéo, vous devez consentir aux Cookies de notre partenaire Youtube Ces cookies permettent de partager ou réagir directement sur les réseaux sociaux auxquels vous êtes connectés ou d'intégrer du contenu initialement posté sur ces réseaux sociaux. Ils permettent aussi aux réseaux sociaux d'utiliser vos visites sur nos sites et applications à des fins de personnalisation et de ciblage publicitaire.
La digitalisation : vers l’excellence opérationnelle et l’amélioration de la vie des collaborateurs
Selon un sondage mené auprès de 5 433 employés de production de sociétés issues de 22 pays, 71 % des personnes interrogées considèrent leurs tâches « comme monotones, dangereuses ou salissantes ». Comment la transformation digitale peut-elle redonner du sens au travail des opérateurs, tout en leur permettant d’améliorer la qualité de leur travail ?
Le rôle de l’expérience client (CX) dans le développement et la mise en œuvre de projets de digitalisation dans l’industrie
Pour optimiser l’expérience collaborateur en usine, il est essentiel que le fournisseur de solutions travaille en étroite coopération avec ses clients, à savoir les responsables des technologies d’exploitation : « Nous suivons cette méthode à la lettre. Notre but étant de fournir les meilleures solutions à nos clients, nous créons une équipe dédiée pour tenir compte de leurs remarques, tout en appliquant les méthodologies relatives à l’expérience client. Nous gardons également à l’esprit leurs attentes, ainsi que les défis propres à leur secteur », explique David Sherman, coach CX chez Orange Business.
Les principales préoccupations des clients sont les suivantes :
- Quel soutien apporter aux techniciens au cours de leurs activités de production afin d’obtenir des produits de meilleure qualité ?
- Quelle assistance leur fournir dans le cadre de leurs activités de maintenance afin d’améliorer leurs résultats ?
- Comment garantir un niveau de sécurité optimal sur les sites industriels ?
Premier défi : soutenir les techniciens dans leurs activités de production et obtenir des produits de meilleure qualité
Il arrive que des anomalies échappent aux procédures standards d’échantillonnage, c’est pourquoi les responsables de contrôle qualité estiment nécessaire de soutenir les techniciens de fabrication, afin d’améliorer leur efficacité et la proactivité quant aux inspections difficiles et à la détection des non-conformités. Les algorithmes d’intelligence artificielle (IA), d’alertes automatiques et de suggestions relatives aux mesures à prendre, sont un bon moyen d’aider les techniciens en détectant automatiquement certaines anomalies.
Par ailleurs, grâce à des technologies de suivi des actifs permettant de géolocaliser et de surveiller les conditions de stockage et de transport des produits fabriqués, les collaborateurs pourront s’assurer que ces derniers sont manipulés avec soin dans les entrepôts et pendant la livraison.
Ces solutions présentent de nombreux avantages pour les sociétés de fabrication :
- Baisse des coûts de fonctionnement sur site (réduction du délai de détection des anomalies et d’analyse de leur origine, ainsi que du temps nécessaire à la formation des opérateurs)
- Atténuation des risques de non-conformité grâce au suivi en temps réel de l’apparition de défauts
- Amélioration de la satisfaction client via la fourniture de produits de meilleure qualité
- Réduction des coûts de service après-vente
Deuxième défi : assister les opérateurs dans leurs activités de maintenance afin d’améliorer leurs résultats
Les temps d’arrêt des machines sont la bête noire des responsables de maintenance. Ils sont pourtant récurrents, en raison de la mauvaise compréhension des paramètres nécessaires au bon fonctionnement des machines. Ce phénomène peut être évité grâce à des capteurs de suivi de ces paramètres (humidité, température, tension, etc.). Les données sont transmises et regroupées sur des tableaux de bord permettant de suivre l’état des machines en temps réel et de donner l’alerte dès qu’un comportement susceptible de provoquer un temps d’arrêt des machines est détecté.
Les responsables souhaitent également assister les techniciens dans leurs opérations de maintenance, notamment pour les tâches les plus complexes, afin d’éviter des interventions coûteuses sur le terrain en cas d’erreur de manipulation. Cela peut être réalisé en équipant les techniciens de lunettes et de casques connectés, leur permettant de visualiser les directives d’exploitation ou de contacter des experts à distance. Ces outils connectés « mains libres » les accompagnent dans la réalisation de leurs missions, de tâches de maintenance, lors des changements d’équipe, etc.
Enfin, les équipes opérationnelles doivent pouvoir connaître rapidement l’emplacement des outils et des pièces détachées dont ils ont besoin, afin de ne pas perdre de temps à les chercher. Ainsi, les technologies de suivi des actifs permettent aux opérateurs de géolocaliser les outils sur l’ensemble des sites de production.
Ces solutions permettront aux entreprises :
- De réduire les coûts relatifs à leurs opérations, à la formation des collaborateurs et aux déplacements d’experts
- D’optimiser l’utilisation des outils de maintenance ainsi que les procédés d’intervention, de suivi et d’audit du travail effectué
- D’améliorer la collaboration et le partage de connaissances entre collègues.
Troisième défi : garantir un niveau de sécurité optimal pour les techniciens sur les sites industriels
Chaque jour, des milliers d’ouvriers et d’entrepreneurs se rendent sur le terrain et accèdent à des sites parfois dangereux, mais leur nombre varie d’un jour à l’autre. C’est pourquoi les responsables HSE (hygiène, santé, environnement) doivent pouvoir les localiser afin d’éviter l’encombrement des différentes zones ou les accès non autorisés. Là aussi, les solutions de suivi des actifs permettent de géolocaliser le personnel et les véhicules de l’entreprise, ainsi que de signaler l’encombrement des différentes zones et les accès interdits.
Les responsables HSE doivent également contrôler l’utilisation des équipements de protection individuelle (lunettes, masques, casques, etc.) par les opérateurs et être en mesure de réagir rapidement en cas d’accident. Les dispositifs de vision par ordinateur (caméras, analyse d’images et de dispositifs d’IA) détectent automatiquement les situations à risque (collaborateur ne portant pas d’équipement de protection ou en situation de détresse) et le signalent à l’agent de supervision.
En outre, les responsables HSE sont chargés de garantir des conditions de travail adéquates, non seulement pour le bien-être des collaborateurs, mais aussi par respect des réglementations en vigueur. Pour ce faire, il leur est possible d’équiper leurs installations de capteurs qui collectent les données relatives à la température, à l’humidité et à la qualité de l’air. Les données collectées sont regroupées sur un tableau de bord, permettant ainsi de donner l’alerte en cas de dépassement des seuils établis.
Grâce à ces outils innovants, les industriels peuvent désormais respecter les règles de sécurité, diminuer le nombre d’accidents, répondre plus rapidement en cas de problème, améliorer le bien-être au travail, assurer la continuité des opérations et atténuer les risques en matière de conformité et de réputation.
Mettre l’accent sur les expériences collaborateur et client lors de projets de digitalisation est un facteur clé de succès, non seulement en matière d’excellence opérationnelle, mais aussi pour l’amélioration de la vie des collaborateurs.
Pour aller plus loin
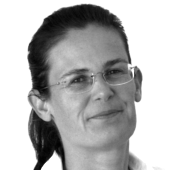