Inspiring, connecting and transforming in the age of AI
We’ll help you take advantage of generative AI’s immense potential and address its challenges.
Inspiring, connecting and transforming in the age of AI
We’ll help you take advantage of generative AI’s immense potential and address its challenges.
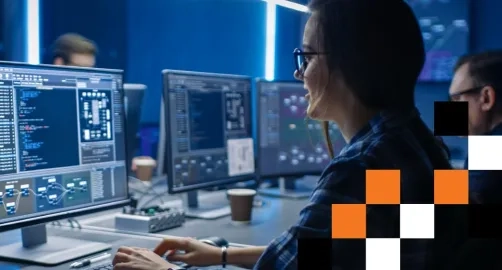
Connectivity, cloud and cybersecurity are the foundations of any digital infrastructure. We have the infrastructure integration capabilities and expertise to expertly design, build and manage your infrastructures.
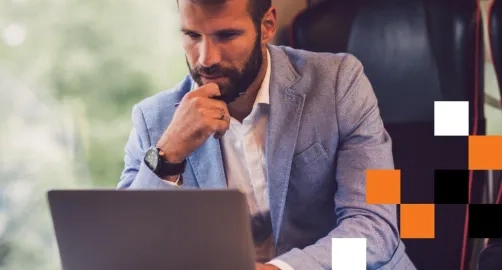
Increase productivity and make it easier for your teams to collaborate. We’ll help you create a sustainable employee experience with new, more collaborative ways of working.
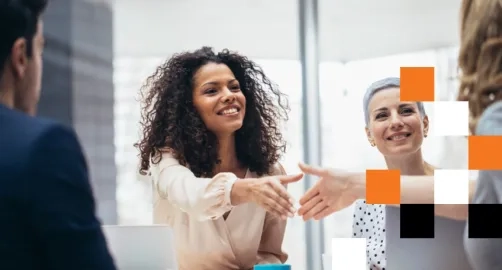
Give your employees the tools to communicate effectively across all your customer-contact touchpoints. We'll guide you through developing a personalized customer relationship model that's innovative, easy to use and perfect for your business.
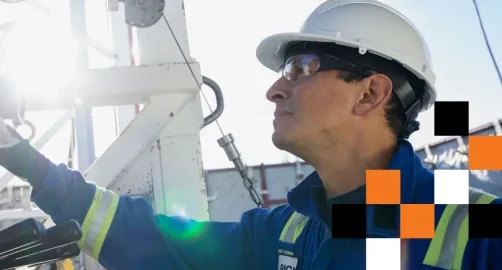
Optimize your production chain and create a safe, autonomous environment for your workers. We’re here to help you revitalize your industrial processes and get ahead with new, cutting-edge connected products.
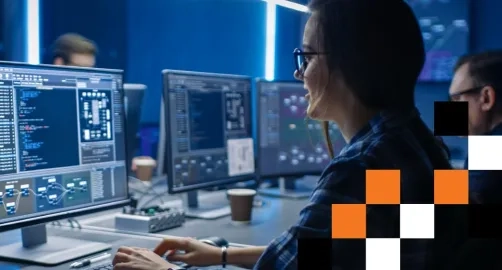
Connectivity, cloud and cybersecurity are the foundations of any digital infrastructure. We have the infrastructure integration capabilities and expertise to expertly design, build and manage your infrastructures.
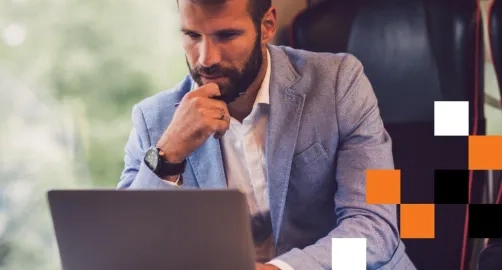
Increase productivity and make it easier for your teams to collaborate. We’ll help you create a sustainable employee experience with new, more collaborative ways of working.
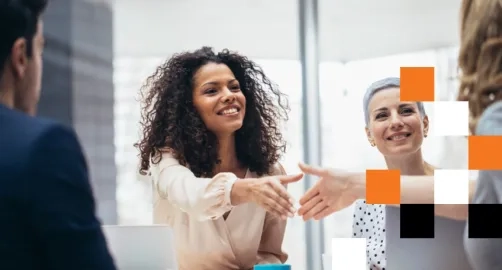
Give your employees the tools to communicate effectively across all your customer-contact touchpoints. We'll guide you through developing a personalized customer relationship model that's innovative, easy to use and perfect for your business.
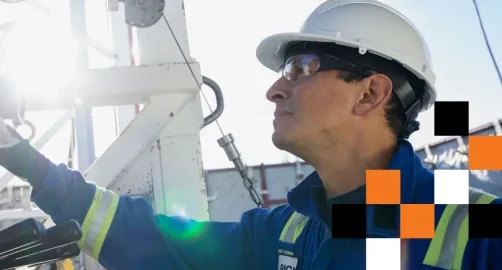
Optimize your production chain and create a safe, autonomous environment for your workers. We’re here to help you revitalize your industrial processes and get ahead with new, cutting-edge connected products.
Pagination
- Page 1
- Next page ›
Our teams are located in over 100 countries, ready to deploy and supervise your networks and digital solutions on a daily basis.